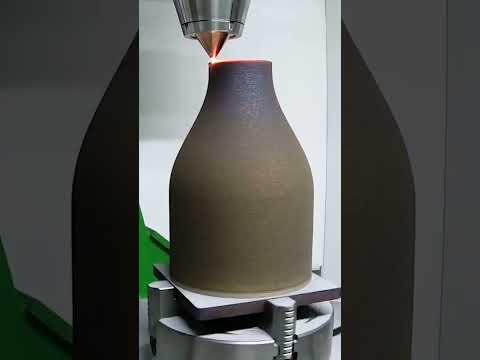
This video shows the additive process of an aerospace nozzle made on a BeAM Magic 800 machine.
It was CAM programmed using hyperMILL ADDITIVE Manufacturing.
4 Considerations to Help You Choose Between Additive and Subtractive Manufacturing Methods
In the most basic sense, manufacturing methods can be separated into two camps: those which are additive and those which are subtractive. Additive methods include fused deposition modeling and stereolithography, which create parts by stacking consecutive layers of material to form the shape of the part from the ground up.
Subtractive methods include machining operations like milling and CNC turning, laser cutting, wire EDM, and carving.
When deciding which manufacturing method to use, there are four broad considerations that will help inform your decision:
1. Material Selection
For Most Plastics: Additive
With additive production, the most common materials are limited to a growing list of plastic materials, including:
ABS (Acrylonitirle butadiene styrene)
PLA (Polylactic Acid)
PVA (Polyvinyl Alcohol Plastic)
Nylon
Resins
material samples
More recently ceramics and metals have also entered the 3D printing scene, significantly broadening the types of parts which can conceivably be 3D printed. However, these materials are currently only printed on specialty machines for a high price, so they’re not yet suitable for most production needs.
Note that parts made for low-volume casting methods can use a 3D printed part to create a silicone mold used for casting in a wide variety of materials.
For More Material Variety: Subtractive
Subtractive methods can utilize a wide variety of materials, including:
Engineering metals, such as aluminum and steel
Wood
Foams, like polystyrene or structural foam
Ceramics
This variety of available materials can give you more flexibility. So if you’re engineering a very large part, for example, you can choose to cut from a piece of foam core, which will be much less expensive than producing a very large 3D printed plastic part.
2. Part Quantity
For Low Volume Production: Additive
For its speed and relative unit cost at low volumes, additive methods are typically well suited for prototype or low volume production runs in the range of one to ten parts. 3D printers can also produce a complete set of different parts all during a single run, something that would be practically impossible to achieve using subtractive methods like a mill or lathe.
For High Volume Production: Subtractive
When you need to produce a large quantity of parts, subtractive methods like machining is still generally the right approach. Modern CNC machining methods are capable of producing a high degree of part-to-part repeatability and can output large volumes of the same part in a relatively short period of time.
Additionally, molds for injection molded plastic components are created using steel dies, which are produced using subtractive manufacturing methods.
3. Part Geometry
For Organic Surfaces and Complex Features: Additive
Although CNC milling machines are constantly improving, additive methods are still the most effective way to produce parts with intricate geometry; 3D printers can produce impossible to machine features, like ‘captured’ components.
Keep in mind that the part accuracy and level of intricacy for parts created with 3D printers will be limited by factors like minimum layer thickness and material type. Higher-end materials and machines may be required to achieve desired levels of feature precision.
For Dimensional Accuracy and Repeatability: Subtractive
When it comes to precision for common functional features, like flat faces, drilled and tapped holes, counterbores, and mating components, subtractive methods will generally produce results with the highest degree of repeatability and dimensional accuracy.
This is primarily because subtractive methods can create parts using very dense, hard materials like steel and aluminum, which can be machined to a very high degree of precision.
4. Project Schedule and Part Revisions
For Faster Lead Times and Iterative Prototyping: Additive
One of the best features of 3D printing is the lead time compared with machined parts. The use of additive technology can shorten your production cycles by iterating and testing revised designs more quickly than would otherwise be possible with one-off machined components.
In contrast, part revisions on machined parts may require changes to programmed tool paths, setup, and number of machining operations – changes which all take significant time.
Best practice here is to plan for several 3D printed iterations of a part design prototype to test fit and function before manufacturing components with machining methods.
#engineering #3dprinting #machining
- Aerospace Nozzle ADDITIVE Manufacturing ( Download)
- Aerospace Nozzle ADDITIVE Manufacturing ( Download)
- Aerospace Nozzle ADDITIVE Manufacturing ( Download)
- hyperMILL ADDITIVE Manufacturing Aerospace Nozzle ( Download)
- The Genius of 3D Printed Rockets ( Download)
- Multi-Material Rocket Nozzle ( Download)
- Additive Manufacturing Process of an Aerospace Part ( Download)
- Aerospace NOZZLE by ADDITIVE MANUFACTURING ( Download)
- Metal 3D Printed Rocket Nozzle, Heat Exchanger + Hydraulic Block ( Download)
- Space Nozzle for Vega-E rocket by Additive Manufacturing with Mixed Powders. ( Download)
- What is Additive Manufacturing ( Download)
- Additive Manufacturing with Mike Cloran ( Download)
- 3D Printing a Titanium Part Created By Artificial Intelligence ( Download)
- Amazing Metal Additive Process ( Download)
- Revolutionizing Aerospace Technology: 3D Printing Nozzles for Rocket Engines ( Download)